An integrated approach to cost optioneering on capital projects
Written by Chloe Smith, Director of Product Management, AVEVA
In the race to decarbonize and future-proof existing assets, industrial organizations are expected to invest up to $130 trillion globally between now and 2027, according to McKinsey. Yet the consultancy warns that few organizations have the right tools or structure to be able to deliver capital expenditure (CAPEX) projects with the necessary speed or efficiency.
Being able to effectively analyze the equipment cost of green- and brownfield projects is fundamental to their successful delivery. Without easy access to verified data, engineers often select plant designs based on gut instinct and previous experience rather than taking a data-led approach that considers economic impact. All too often this can lead to final investment decisions (FID) being made on an inaccurate picture of expected costs and design approach.
Optioneering and process simulation
Many engineers use cost optioneering to gain useful insights into how different plant configurations could impact the relative capital cost of procuring equipment and materials. Traditionally, they have relied on spreadsheets to calculate the economic case for various design options. These insights are used to qualify the project during front-end engineering and design (FEED) stages and provide the foundations for cost control. This approach can be time-consuming and often inaccurate, with engineers entering “best-guess” values. It is also disjointed from other process simulation activities such as equipment sizing.
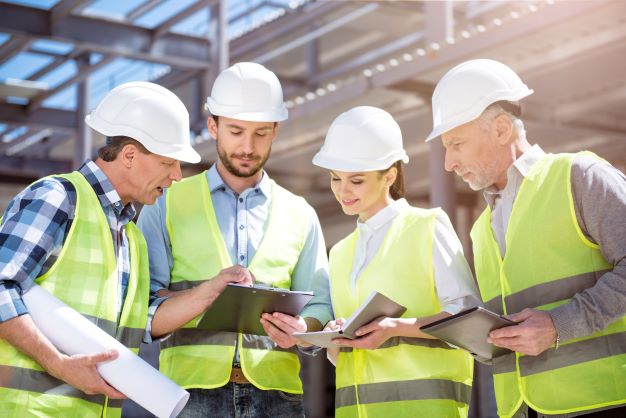
Cloud-enabled technology now allows optioneering to be fully integrated on a single, AI-infused process simulation platform. Connecting all process engineering data in a single, trusted hub unlocks insights faster and delivers greater flexibility. Inbuilt optimizers help find the best designs. It enables engineers to generate cost estimate analysis from plant designs and compare relative costs from early in the design phase. For example, one approach may have higher capital costs but lower operating costs while a different option may have lower capital costs and higher operating costs.
These cost insights can be supported by process simulations to identify the strongest options from both a design and cost perspective. Armed with these insights, engineers can collaborate early in the design phase to minimize risks.
An integral tool for a sustainable future
As the energy sector accelerates its transition to net zero, investors are increasingly being asked to back low carbon plants including hydrogen and carbon capture, utilization and storage facilities. Operators and their engineering, procurement, and construction (EPC) counterparts must not only be able to provide return on investment (ROI) assurances, but also demonstrate sustainability metrics.
AVEVA™ Process Simulation has an integrated optioneering tool that eliminates the guesswork of capital and operating project cost analysis, enabling engineers to make trusted decisions within a single platform. It also allows engineers to understand the sustainability impacts of design alternatives.
Carbon Capture, Utilization and Storage (CCUS) company Airbridge recently built a case for investors and potential industrial clients by providing detailed modeling of its patented technology to accurately simulate the process and model how it could be scaled for commercialization. Solutions included AVEVA™ Process Simulation, AVEVA™ Edge, and AVEVA™ Insight.