It’s time to turn your brownfield plants green
Written by Vanessa Erickson, Global Marketing Lead, AVEVA
There’s no disputing that the digitalization of industrial capital expenditure projects is transforming how we work and collaborate – helping deliver projects quicker, and more cost effectively. But delivering value is only half of the story. Now, driving forth environmental performance has become another, equally important driver in setting the industrial outperformers apart.
This means that industrial operators face a double conundrum as they plan for the plants and ships of the future: How to improve the profitability of their capital assets while also meeting increasing environmental, social, and governmental (ESG) targets?
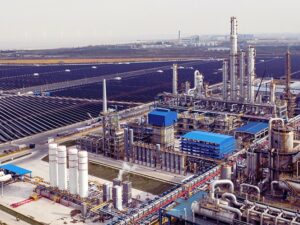
The connected plant of the future is nearly here. Are you ready?
Read our Engineering the Plant of the Future whitepaper to learn more how your plants can meet the future with innovation, flexibility and resilience.
Existing assets are prime grounds for achieving both objectives. They require significantly less investment than a new asset, freeing up capital for digital transformation initiatives which unlock smart operational improvements that can benefit your bottom line and reduce your carbon footprint. As a result, the number of brownfield capital expenditure projects is on the rise with over $600 billion of brownfield and revamp investment planned in the US over the next 5 years.
So, how can companies maintain regulatory compliance, reduce emissions, and boost operational capacity and efficiency? When the plant is new, the answer is simple – leverage data-driven insights from digital twins – but on a facility built years before digital systems were commonplace, where do you begin?
A brownfield capital project faces many of the same challenges as a greenfield project. Siloed teams, ineffective information sharing and constant project changes that lead to schedule and cost overruns. However, on existing assets, teams work within the constraints of an operating plant, which creates added pressure to minimize downtime for the project and rapid ramp-up back to capacity. That’s why it’s especially important to approach your brownfield project in a data-centric way, using a single hub for the engineering tools and data they create. This approach provides an intelligent digital twin hosted securely in the cloud to create transparency that helps teams to deliver projects on-time and schedule, while also shortening handover time, improving its quality, and minimizing unplanned future maintenance downtime.
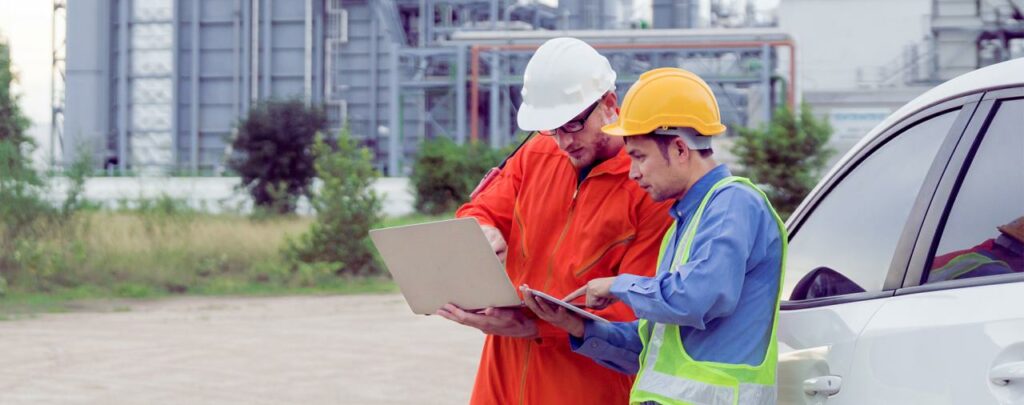
At the heart of any reliable digital twin is quality data. While greenfield projects have the luxury of gathering data right from the start, brownfield projects need to play catch-up by creating a digital representation of the existing asset. All 1D and 2D documents and schematics need to be digitized to create the data hub, and then tagged and linked to a 3D laser scan of the asset to build a fully contextualized digital twin of the asset as it exists today.
From here, unified engineering tools can be used to align all teams around the single platform of verified data – connecting workers, data, processes and decisions. Engineers can segment the information exactly how and when they need it. Managers gain end-to-end visibility and control of every phase of the project while engineering time is freed from sourcing and checking data to being able to identify new and better ways of working to optimize project delivery and operations.
Perhaps one of the most valuable opportunities in digitally transforming your existing plants is the opportunity to test designs far before they’re implemented. By integrating process simulation with the engineering processes, teams can test various design processes and select the most sustainable, efficient, and productive possible version. This holistic approach unlocks instant return by informing the project delivery process itself, while laying the groundwork to empower operations and provide lasting value in the future.