How industrial service providers are increasing operational efficiency with remote monitoring
Written by Daniel Gaeta, Product Marketing Manager, AVEVA Data Hub
The promise of real-time asset monitoring
In an increasingly competitive market, industrial manufacturers, suppliers, and service providers are looking for new and improved ways to deliver value-added services to maximize operational efficiency. Real-time operations data can be the key to unlocking these new revenue streams by providing performance data that facilitates predictive maintenance and optimization for operations close at hand and far away. With remote access to this real-time data from assets, a company can optimize its resource usage, efficiency, health and safety, as well as productivity.
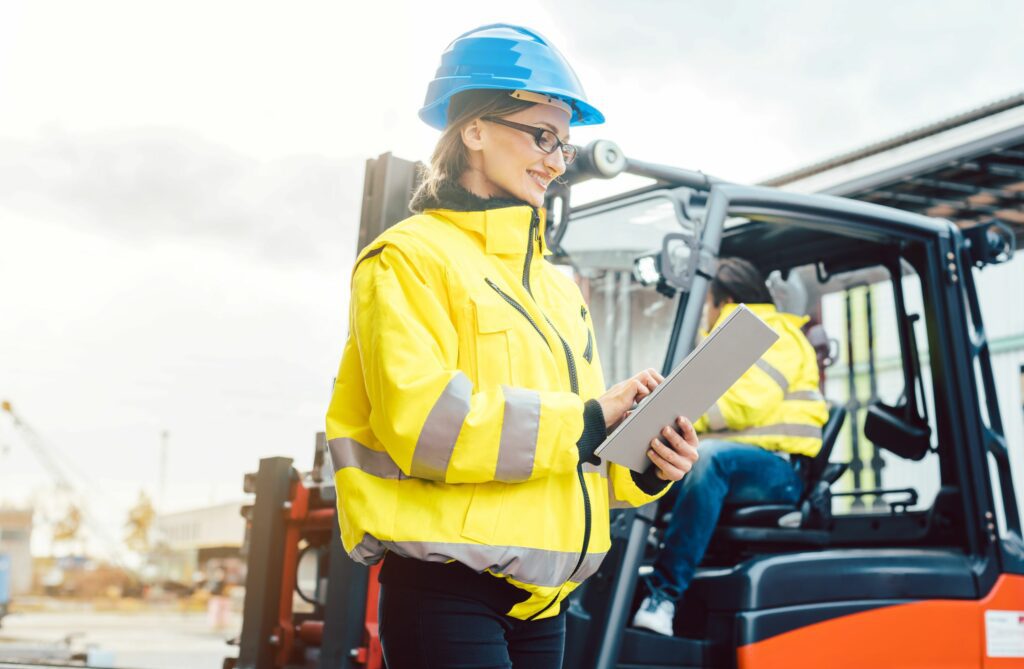
The rich resource of performance data
Real-time asset monitoring offers a rich stream of performance data. This data, when securely made available to external stakeholders, can improve operations across businesses, reducing existing costs and offering the possibility for models to optimize future operations.
Real-time data has wide applicability across industries. Suppliers in the chemicals industry rely on data from mobile delivery trucks to increase their billing accuracy and improve decision-making at sites without network connectivity. Energy transmission and distribution companies make their systems more efficient by remotely monitoring batteries and solar panels for smart grid management.
In a recent success story, RHI Magnesita, a world-leading refractory materials supplier for high-temperature industrial processes, used AVEVA™ Data Hub to enable real-time monitoring of its electric arc furnaces. The company relies on performance data to carry out predictive maintenance for its customers across the globe, so having access to real-time data remotely was a key requirement to help them improve their services. For a product like its electric arc furnaces, precise predictive maintenance is extremely important. The furnace walls need to stand up against extreme heat—upwards of 1200°C—to prevent liquid steel from endangering plant personnel. At the same time, if RHI Magnesita takes one of these machines offline too early, it can cost its clients tens of thousands of Euros per day.
Since implementing a “connected machines architecture”—using AVEVA Data Hub and AVEVA™ PI System™—RHI Magnesita has improved its accuracy in tracking materials. It now predicts refractory consumption for six months with an accuracy of more than 80%.
RHI Magnesita passes on the benefits of this new analysis to its clients. Its predictive maintenance empowers the company to allocate service parts and workers in advance to relieve potential supply bottlenecks, prevent unexpected outages, and generally reduce downtime. The company even offers its clients advice on when to change components and when to reorder refractory materials, increasing coordination and efficiency for both supplier and customer.
As the RHI Magnesita case study demonstrates, if a company can remotely access real-time data, it means increased product reliability, better management, and reduced costs with availability guarantees. Both suppliers and customers share the benefit of the operational efficiency that real-time performance data enables.
The enablement of remote monitoring may even generate additional revenue streams with add-on services, which can set companies apart from competitors. Industrial manufacturers could even start to leverage the data collected to improve the design and engineering of their products.
Sifting through remote data requires the right solution
Real-time asset monitoring demands vast quantities of data, which requires remote data collection to achieve maximum efficiency. The development of less expensive sensors, better software, and improved connectivity empowers companies to collect operations data that was once stranded beyond the traditional control network. With the right data management solution, they can collect edge data easily and cost-effectively.
Service providers need a solution that can capture and contextualize all the relevant data including the necessary descriptors, rollups, drill-downs, and relationships, to give the raw data meaningful context, so analysts can act on it. The right data management solution must eliminate barriers to secure data-sharing. A shared data ecosystem in which partners securely share data is foundational to developing the connected industry of the future.
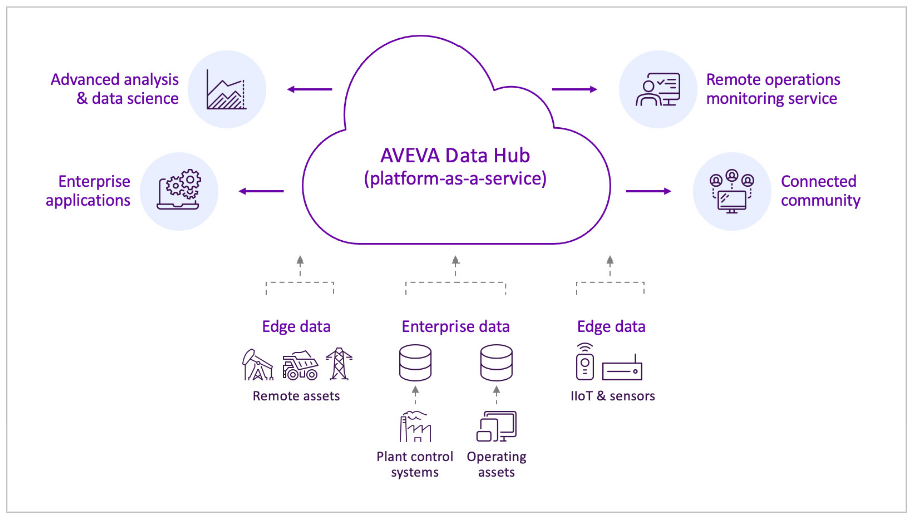
AVEVA Data Hub
AVEVA Data Hub is a tool made for just this opportunity. It can reduce the cost, effort, and risk associated with monitoring assets located outside the primary operations network. A cloud-native data management service, AVEVA Data Hub offers combined solutions that can easily pull real-time data from industrial Internet of Things (IIoT) devices, sensors, and legacy assets. It then aggregates the information in a cloud-based data hub that securely supports authorized data users with contextualized data in any location, inside or outside the company. With AVEVA Data Hub, equipment suppliers and service providers have real-time access to customer data in its original fidelity—for faster, more accurate services with less expense.
AVEVA Data Hub accelerates the timeline for realizing the value of real-time asset monitoring. It requires neither development nor integration, and it scales as needed. It’s already natively integrated with AVEVA PI System and has robust security measures that ensure reliability and security as data moves across networks and enterprises. Furthermore, it’s maintained by AVEVA, reducing the need for a large investment in IT and maintenance.